FLEX-AUGER® PLUS System Offers an Economical Conveying Solution
Brock’s FLEX-AUGER® PLUS Material Conveying System has been an efficient and economical solution for industrial applications for over 40 years. The FLEX-AUGER PLUS System is designed exclusively for handling free-flowing industrial materials to save valuable floor space, as well as the labor costs associated with moving raw materials around the plant.
More
Brock’s FLEX-AUGER® PLUS Material Conveying System is compatible with:
- Plastic pellets, compounds, chips, powders and regrind
- Walnut shell flour
- Dry sawdust
- Starch
- Clay pellets
- Ground paper currency
- Tomato waste
- Wood pellets
- Rice hulls
- Calcium carbonate
If you have questions about conveying your free-flowing material, contact Brock’s engineering department to learn more about testing your material and obtaining a conveying system design.
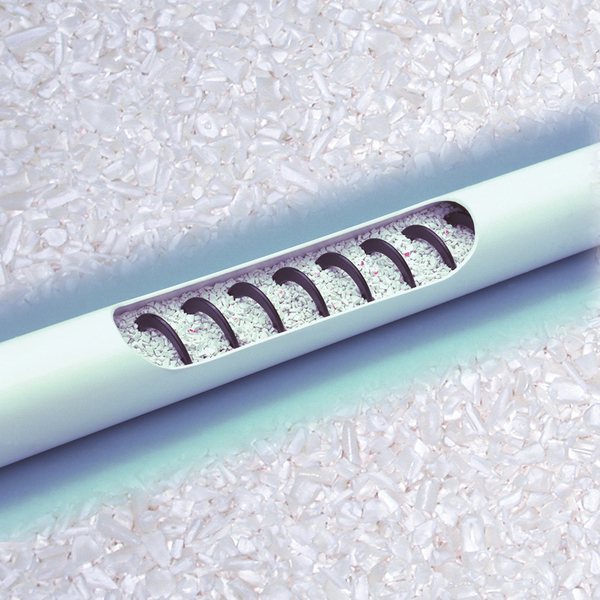
A single-piece spiral steel auger turns inside PVC tubing for use in conveying raw materials in or out of your plant and up, down, or around corners.
This design has fewer parts and components for greater dependability and also costs less to install than other systems.
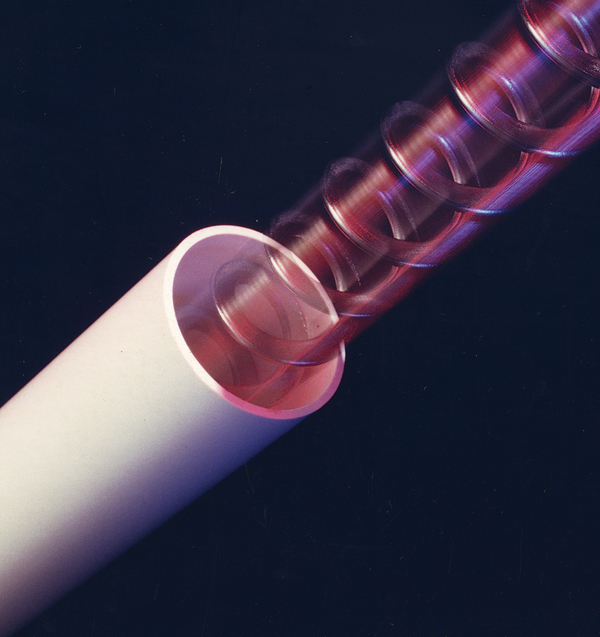
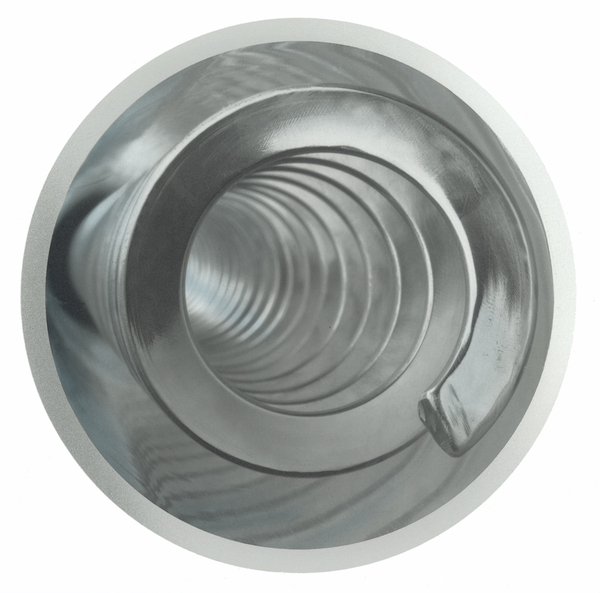
Brock’s FLEX-AUGER® PLUS Material Conveying System requires less horsepower, saving energy. It is capable of running continuously or on demand to save energy and also offers instant, full-load start-up to save time. The system runs quiet to reduce plant noise levels.
Options include:
- Outlet drops
- Direct-drive motors with gear heads
- Discharge boots for silos (single or twin outlet)
- Level control monitors that permit energy-saving, automatic operation
- Steel tubing can be used instead of PVC when hot or abrasive materials are to be conveyed
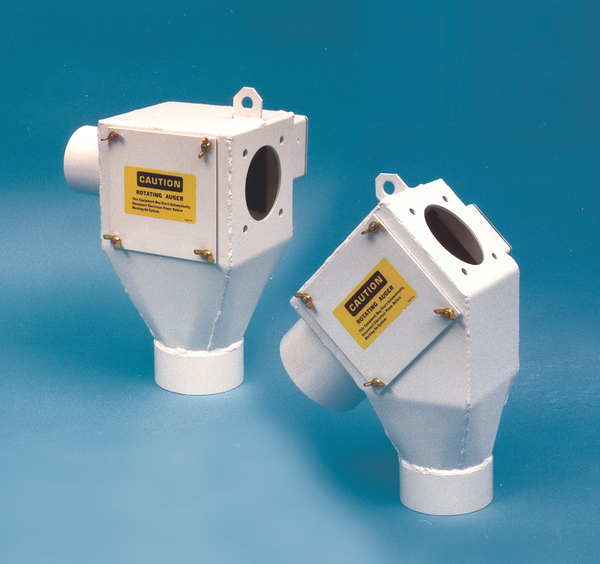
FLEX-AUGER® PLUS Capacity Chart
Model | Tube Outside Diameter | Standard Maximum Length | Extension Length* | Maximum Corner Radius | Maximum Capacity per Minute | Maximum Capacity per Hour | Maximum Delivery Rate** | Particle Diameter |
---|---|---|---|---|---|---|---|---|
2000 | 2.95 in. (75 mm) | 120 ft. (36.5 m) | 145 ft. (44.2 m) | 5 ft. (1.5 m) | 1.25 ft3 (.04 m3) | 75 ft3 (2.1 m3) | 50 lbs. (22.7 kg) | .13 in. (3.3 mm) |
2500 | 3.5 in. (89 mm) | 100 ft. (30.5 m) | 115 ft. (35.1 m) | 5 ft. (1.5 m) | 1.25 ft3 (.04 m3) | 75 ft3 (2.1 m3) | 50 lbs. (22.7 kg) | .40 in. (10.2 mm) |
3000 | 3.5 in. (89 mm) | 100 ft. (30.5 m) | 115 ft. (35.1 m) | 5 ft. (1.5 m) | 2.5 ft3 (.07 m3) | 150 ft3 (4.3 m3) | 100 lbs. (45.5 kg) | .25 in. (6.4 mm) |
6500 | 4.5 in. (115 mm) | 100 ft. (30.5 m) | 115 ft. (35.1 m) | 5 ft. (1.5 m) | 5.5 ft3 (16 m3) | 330 ft3 (9.4 m3) | 220 lbs. (99.8 kg) | .40 in. (10.2 mm) |
* By using extension boot at motor end of first auger, plus additional tube, auger, and motor.
** Calculated at 40 pounds per cubic foot (640 kilograms per cubic meter) material density at 348 RPM.
NOTE: Testing of materials is recommended for verification of conveying capacity and power requirements for all models.
In the pursuit of LEADERSHIP THRUOGH INNOVATION®, Brock reserves the right to change specifications without prior notice.